
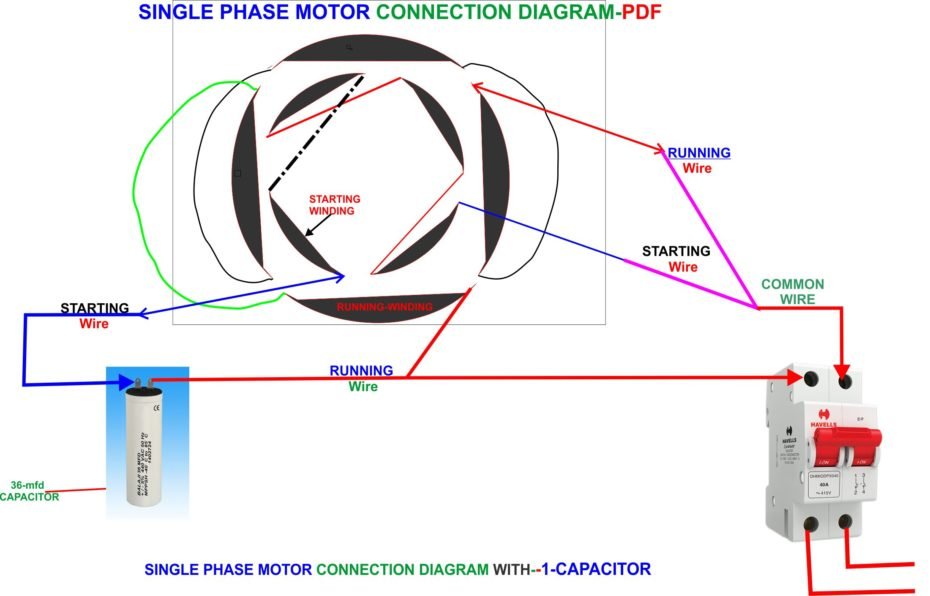
The winding is not simple to wind and very expensive machinery is required to keep the labor at a minimum. This type of design has a very high reluctance cogging torque and very large end turns which contribute to I R losses. This results in a less effective second dip of varnish.īecause we want to ensure adequate varnish coverage, Dreisilker’s quality standards denote that the windings must be cool before the second dip. (3) phase (4) pole brushless motors are designed using (12) slot laminations with a (3) slot pitch distributed winding. 0.021 /m length and per mm2 cross section area at 750C. Lmts 2L + 2.3 + 0.24 m where L and are shown in m. Length of mean turn of stator winding It can be calculated from following equation. Because the windings are still hot during the second dip, the varnish becomes more viscous and runs off the motor easily. Stator winding resistance The stator winding resistance per phase mts s s s LT r a where Lmts length of mean turn of stator winding.
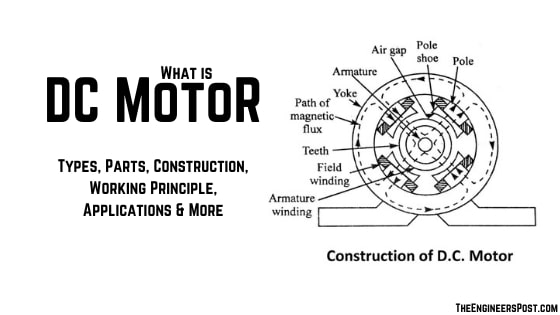
Many repair shops do not allow the windings to cool once they are cured in the oven after the first dip and before the motor is dipped a second time. provide the student with practical information for winding, repaiTina, and troubleshooting alternat:ng current and direct current motors, and controllers. Typically, a new motor winding should be dipped twice (double dip and bake) to ensure the varnish fully covers the windings.

There are four types of varnishing methods that we will describe below: Dip and Bake Epoxy Varnishing, Trickle Varnishing, Vacuum Pressure Impregnation, and Ultra-Sealed Winding.ĭip and Bake is a standard varnishing technique where the motor windings are dipped into a varnish tank and then set to cure in an oven. This insulation protects the windings from contamination, shorting electrically, and also make the windings more mechanically rigid. After a motor is rewound, the windings must be further insulated with resin or varnish.
